Hardwood flooring still in process!
We are still working on getting the hardwood flooring installed in our kitchen. It has been a long, yet rewarding process. I really think this is because you can "see" your progress! You work and work, and it takes forever--yet line by line, you see your efforts paying off!! I have run into a couple of design issues. The island that was in the kitchen originally was modified by the PO. BLEH! Although it has solid oak doors just like the cabinets, the sides and back were faux oak. Over this, the PO secured cabinet grade plywood, but didn't do a very good job of it. It was stained by the PO in an effort to match the oak doors, but ALAS-- PO was obviously color blind! I painted the sides and back, then decided to just get rid of it. I drug it out into the garage, bought a lovely, distressed, furniture style kitchen island, and installed it. Now, I am thinking of taking that back to the store, and re-working the original island. WHEW!

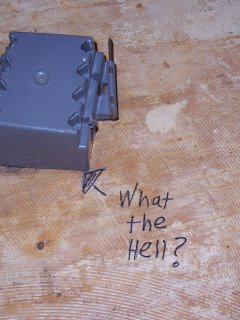